Destylator przemysłowy to zaawansowane urządzenie, które służy do separacji cieczy na podstawie różnicy w temperaturze wrzenia poszczególnych składników. W procesie tym wykorzystuje się zjawisko destylacji, które polega na podgrzewaniu cieczy do momentu, w którym zaczyna ona parować, a następnie schładzaniu pary, aby skondensować ją z powrotem w ciecz. Destylatory przemysłowe są wykorzystywane w różnych branżach, takich jak przemysł chemiczny, petrochemiczny czy spożywczy. W zależności od zastosowania, mogą mieć różne konstrukcje i rozmiary. Na przykład, w przemyśle alkoholowym stosuje się destylatory kolumnowe, które pozwalają na uzyskanie wysokiej czystości produktu końcowego. W przypadku produkcji olejów eterycznych często używa się destylacji parowej.
Jakie są rodzaje destylatorów przemysłowych i ich zastosowanie
W przemyśle można spotkać wiele rodzajów destylatorów, które różnią się zarówno konstrukcją, jak i zastosowaniem. Najpopularniejsze typy to destylatory prostokątne, kolumnowe oraz wirujące. Destylatory prostokątne charakteryzują się prostą budową i są najczęściej używane w małych zakładach produkcyjnych. Z kolei destylatory kolumnowe umożliwiają uzyskanie wyższej czystości produktów dzięki wielokrotnemu skraplaniu pary w kolumnie frakcyjnej. W przemyśle chemicznym często stosuje się także destylatory wirujące, które pozwalają na szybszą separację składników przez wykorzystanie siły odśrodkowej. Każdy z tych typów ma swoje specyficzne zastosowanie, które zależy od rodzaju przetwarzanej substancji oraz wymagań dotyczących jakości produktu końcowego.
Jakie są kluczowe elementy budowy destylatora przemysłowego
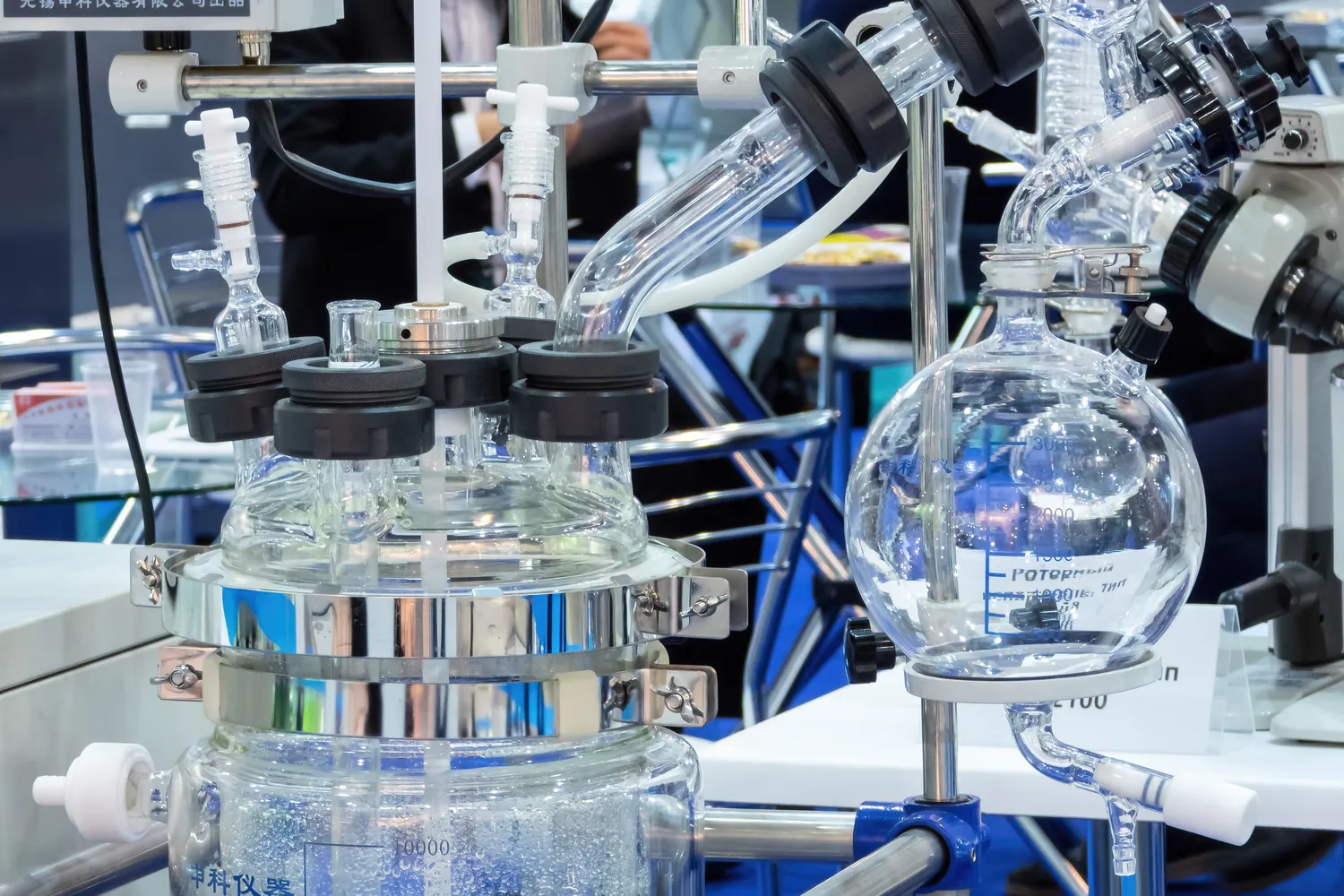
Budowa destylatora przemysłowego opiera się na kilku kluczowych elementach, które współpracują ze sobą w celu efektywnego przeprowadzenia procesu destylacji. Podstawowymi komponentami są zbiornik na ciecz surową, elementy grzewcze oraz system chłodzenia. Zbiornik jest miejscem, gdzie umieszczana jest ciecz do destylacji, a jego konstrukcja musi być dostosowana do rodzaju przetwarzanej substancji oraz jej właściwości fizycznych. Elementy grzewcze mogą być różnego rodzaju – od elektrycznych po parowe – i mają za zadanie podgrzać ciecz do odpowiedniej temperatury wrzenia. System chłodzenia natomiast odpowiada za kondensację pary powstałej podczas procesu destylacji. Ważnym elementem jest także kolumna frakcyjna, która umożliwia wielokrotne skraplanie pary i tym samym zwiększa efektywność separacji składników.
Jakie są korzyści z używania destylatorów przemysłowych
Używanie destylatorów przemysłowych przynosi wiele korzyści zarówno dla producentów, jak i dla konsumentów. Przede wszystkim proces destylacji pozwala na uzyskanie wysokiej czystości produktów końcowych, co jest niezwykle istotne w branżach takich jak farmaceutyka czy przemysł spożywczy. Dzięki zastosowaniu nowoczesnych technologii możliwe jest również zwiększenie wydajności produkcji oraz redukcja kosztów operacyjnych. Destylatory przemysłowe umożliwiają także efektywne odzyskiwanie surowców wtórnych, co przyczynia się do zmniejszenia negatywnego wpływu na środowisko naturalne. Dodatkowo nowoczesne urządzenia często wyposażone są w systemy monitorowania jakości produktów oraz automatyzacji procesów, co zwiększa bezpieczeństwo pracy i minimalizuje ryzyko błędów ludzkich.
Jakie są najnowsze technologie w destylacji przemysłowej
W ostatnich latach nastąpił znaczący postęp w technologii destylacji przemysłowej, co przyczyniło się do zwiększenia efektywności i jakości procesów produkcyjnych. Jednym z najważniejszych trendów jest zastosowanie technologii membranowych, które pozwalają na separację składników bez konieczności podgrzewania cieczy. Dzięki temu można zaoszczędzić energię oraz zmniejszyć emisję gazów cieplarnianych. Innym innowacyjnym rozwiązaniem są destylatory z systemem odzysku ciepła, które wykorzystują energię z pary skraplającej się do podgrzewania cieczy surowej. Takie podejście nie tylko obniża koszty operacyjne, ale także zwiększa efektywność całego procesu. Warto również wspomnieć o automatyzacji procesów destylacyjnych, która pozwala na zdalne monitorowanie i kontrolowanie parametrów pracy urządzeń.
Jakie są wyzwania związane z użytkowaniem destylatorów przemysłowych
Mimo licznych korzyści, użytkowanie destylatorów przemysłowych wiąże się także z pewnymi wyzwaniami. Jednym z głównych problemów jest konieczność zapewnienia odpowiedniej konserwacji i serwisowania urządzeń, aby uniknąć awarii i przestojów w produkcji. Wysokie temperatury oraz agresywne chemikalia mogą prowadzić do szybszego zużycia elementów konstrukcyjnych, co wymaga regularnych przeglądów i wymiany części. Kolejnym wyzwaniem jest zarządzanie odpadami powstającymi w trakcie procesu destylacji. Wiele substancji chemicznych może być szkodliwych dla środowiska, dlatego ważne jest wdrożenie odpowiednich procedur ich utylizacji. Dodatkowo, w obliczu rosnących wymagań dotyczących ochrony środowiska i zrównoważonego rozwoju, przedsiębiorstwa muszą inwestować w technologie minimalizujące negatywny wpływ na otoczenie.
Jakie są zastosowania destylatorów przemysłowych w różnych branżach
Destylatory przemysłowe znajdują szerokie zastosowanie w wielu branżach, co czyni je niezwykle wszechstronnymi urządzeniami. W przemyśle chemicznym służą do separacji różnych substancji chemicznych, takich jak rozpuszczalniki czy kwasy. W branży petrochemicznej wykorzystywane są do rafinacji ropy naftowej oraz produkcji paliw. Destylatory kolumnowe są szczególnie popularne w produkcji alkoholi wysokoprocentowych, gdzie kluczowe jest uzyskanie wysokiej czystości etanolu. W przemyśle spożywczym stosowane są do produkcji olejków eterycznych oraz aromatów, a także do oczyszczania soków owocowych. W farmaceutyce destylacja jest niezbędna do uzyskiwania czystych substancji czynnych wykorzystywanych w lekach. Ponadto destylatory znajdują zastosowanie w przemyśle kosmetycznym, gdzie służą do produkcji esencji zapachowych oraz składników aktywnych w kosmetykach.
Jakie są kluczowe czynniki wpływające na efektywność destylacji
Efektywność procesu destylacji zależy od wielu czynników, które należy uwzględnić podczas projektowania i eksploatacji destylatora przemysłowego. Pierwszym z nich jest temperatura wrzenia poszczególnych składników mieszanki – im większa różnica między nimi, tym łatwiejsze będzie ich oddzielenie. Ważnym elementem jest także ciśnienie panujące w systemie; obniżenie ciśnienia może prowadzić do zmniejszenia temperatury wrzenia substancji, co ułatwia proces separacji. Kolejnym czynnikiem jest czas kontaktu pary z cieczą – dłuższy czas sprzyja lepszemu oddzieleniu składników o podobnych temperaturach wrzenia. Również konstrukcja kolumny frakcyjnej ma znaczenie; jej wysokość oraz liczba teoretycznych półek wpływają na efektywność separacji.
Jakie są przyszłościowe kierunki rozwoju technologii destylacyjnej
Przyszłość technologii destylacyjnej wydaje się obiecująca dzięki ciągłemu rozwojowi innowacyjnych rozwiązań oraz rosnącemu zainteresowaniu zrównoważonym rozwojem. Jednym z kluczowych kierunków jest dalsza automatyzacja procesów produkcyjnych, która pozwoli na jeszcze bardziej precyzyjne kontrolowanie parametrów pracy urządzeń oraz optymalizację zużycia energii i surowców. W miarę wzrostu znaczenia ochrony środowiska coraz więcej firm inwestuje w technologie minimalizujące emisję gazów cieplarnianych oraz odpady produkcyjne związane z procesem destylacji. Możliwe jest również rozwijanie nowych metod separacji, takich jak ekstrakcja cieczy czy adsorpcja, które mogą stanowić alternatywę dla tradycyjnej destylacji w niektórych zastosowaniach.
Jakie są najlepsze praktyki dotyczące obsługi i konserwacji destylatorów
Aby zapewnić długotrwałe i efektywne działanie destylatorów przemysłowych, istotne jest przestrzeganie najlepszych praktyk dotyczących ich obsługi i konserwacji. Regularne przeglądy techniczne powinny być przeprowadzane zgodnie z zaleceniami producenta oraz obowiązującymi normami bezpieczeństwa. Ważne jest również monitorowanie parametrów pracy urządzenia, takich jak temperatura czy ciśnienie, aby szybko reagować na ewentualne nieprawidłowości. Czyszczenie elementów wewnętrznych powinno być realizowane zgodnie z harmonogramem ustalonym przez specjalistów; zaniedbania mogą prowadzić do osadzania się zanieczyszczeń i obniżenia efektywności procesu destylacji. Pracownicy obsługujący urządzenia powinni być odpowiednio przeszkoleni w zakresie ich działania oraz zasad bezpieczeństwa pracy.
Jakie są najczęstsze błędy przy obsłudze destylatorów przemysłowych
Podczas obsługi destylatorów przemysłowych mogą wystąpić różne błędy, które mogą negatywnie wpłynąć na efektywność procesu oraz jakość produktu końcowego. Jednym z najczęstszych błędów jest niewłaściwe ustawienie parametrów pracy, takich jak temperatura czy ciśnienie, co może prowadzić do nieefektywnego oddzielania składników. Kolejnym problemem jest brak regularnej konserwacji i przeglądów technicznych, co może skutkować awariami i przestojami w produkcji. Zbyt rzadkie czyszczenie elementów wewnętrznych destylatora może prowadzić do osadzania się zanieczyszczeń, co obniża wydajność i jakość destylacji. Ważne jest także, aby pracownicy byli odpowiednio przeszkoleni i świadomi zasad bezpieczeństwa, ponieważ niewłaściwe postępowanie może prowadzić do poważnych wypadków.