Budowa maszyn pneumatycznych opiera się na kilku kluczowych elementach, które współdziałają ze sobą, aby zapewnić efektywne działanie systemu. Wśród najważniejszych komponentów można wymienić sprężarki, które są odpowiedzialne za generowanie sprężonego powietrza. Sprężarki mogą być różnego rodzaju, w tym tłokowe, śrubowe oraz wirnikowe, a ich wybór zależy od specyfikacji aplikacji. Kolejnym istotnym elementem są zbiorniki na sprężone powietrze, które magazynują energię i stabilizują ciśnienie w systemie. Rury i przewody pneumatyczne również odgrywają kluczową rolę, ponieważ transportują sprężone powietrze do poszczególnych komponentów maszyny. Warto również zwrócić uwagę na siłowniki pneumatyczne, które przekształcają energię sprężonego powietrza w ruch mechaniczny. Oprócz tego niezbędne są zawory sterujące, które regulują przepływ powietrza oraz ciśnienia w systemie.
Jakie są zalety i wady maszyn pneumatycznych
Maszyny pneumatyczne mają wiele zalet, które przyciągają uwagę inżynierów oraz przedsiębiorców. Przede wszystkim charakteryzują się one prostotą budowy oraz łatwością w obsłudze, co sprawia, że są popularnym wyborem w wielu branżach przemysłowych. Dzięki zastosowaniu sprężonego powietrza jako medium roboczego, maszyny te są stosunkowo bezpieczne w użytkowaniu, ponieważ nie ma ryzyka wycieków substancji chemicznych czy olejów. Dodatkowo, maszyny pneumatyczne są zazwyczaj lżejsze od ich hydraulicznych odpowiedników, co ułatwia ich transport i instalację. Niemniej jednak istnieją również pewne wady związane z ich eksploatacją. Wysokie koszty energii potrzebnej do sprężania powietrza mogą wpływać na rentowność całego procesu produkcyjnego. Ponadto, wydajność maszyn pneumatycznych może być ograniczona przez straty ciśnienia w systemie oraz konieczność regularnej konserwacji komponentów, takich jak filtry czy smarownice.
Jakie zastosowania mają maszyny pneumatyczne w przemyśle
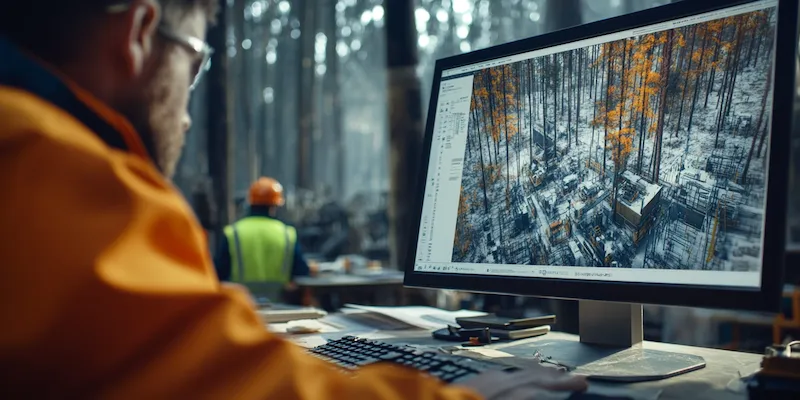
Maszyny pneumatyczne znajdują szerokie zastosowanie w różnych dziedzinach przemysłu ze względu na swoją wszechstronność i efektywność. W branży produkcyjnej wykorzystuje się je do automatyzacji procesów montażowych oraz pakowania produktów. Siłowniki pneumatyczne często stosowane są do napędu robotów przemysłowych, co zwiększa precyzję i szybkość wykonywanych operacji. W przemyśle motoryzacyjnym maszyny pneumatyczne są używane do malowania karoserii oraz montażu części samochodowych dzięki swojej zdolności do pracy w trudnych warunkach. Kolejnym obszarem zastosowań jest przemysł spożywczy, gdzie wykorzystuje się je do transportu surowców oraz pakowania gotowych produktów. Maszyny pneumatyczne znajdują również zastosowanie w branży budowlanej, gdzie służą do obsługi narzędzi ręcznych oraz urządzeń takich jak młoty udarowe czy wiertnice.
Jakie są nowoczesne technologie w budowie maszyn pneumatycznych
Nowoczesne technologie znacząco wpłynęły na rozwój budowy maszyn pneumatycznych, prowadząc do wzrostu ich wydajności oraz niezawodności. W ostatnich latach zauważalny jest trend integracji systemów pneumatycznych z automatyką przemysłową oraz Internetem Rzeczy (IoT). Dzięki temu możliwe jest zdalne monitorowanie stanu maszyn oraz optymalizacja procesów produkcyjnych w czasie rzeczywistym. Nowoczesne czujniki pozwalają na precyzyjne pomiary ciśnienia oraz przepływu powietrza, co umożliwia lepsze zarządzanie energią i minimalizację strat. Dodatkowo rozwój materiałów kompozytowych i lekkich stopów metali przyczynił się do zmniejszenia masy komponentów maszyn pneumatycznych, co z kolei wpływa na ich mobilność i łatwość instalacji. Wprowadzenie technologii cyfrowych pozwala także na symulacje komputerowe podczas projektowania nowych rozwiązań, co zwiększa efektywność procesu inżynieryjnego. Warto również zwrócić uwagę na rozwój systemów serwisowych opartych na sztucznej inteligencji, które mogą przewidywać awarie i sugerować działania konserwacyjne zanim do nich dojdzie.
Jakie są najczęściej występujące problemy w maszynach pneumatycznych
Maszyny pneumatyczne, mimo swojej niezawodności, mogą napotykać różne problemy, które wpływają na ich wydajność i funkcjonalność. Jednym z najczęstszych problemów jest wyciek sprężonego powietrza, który może prowadzić do znacznych strat energii oraz obniżenia efektywności całego systemu. Wyciek może występować w miejscach połączeń rur, zaworów czy uszczelek, dlatego regularna kontrola i konserwacja tych elementów są kluczowe. Innym istotnym problemem jest zanieczyszczenie sprężonego powietrza, które może prowadzić do uszkodzenia siłowników i innych komponentów. Zanieczyszczenia mogą pochodzić z otoczenia lub być wynikiem zużycia elementów maszyny. W takich przypadkach stosowanie filtrów oraz systemów odwadniających jest niezbędne dla zapewnienia czystości medium roboczego. Dodatkowo, niewłaściwe ustawienie ciśnienia roboczego może prowadzić do nieprawidłowego działania maszyn, co skutkuje spadkiem wydajności oraz zwiększeniem ryzyka awarii. Warto również zwrócić uwagę na problemy związane z elektroniką sterującą, które mogą wpływać na precyzyjność działania systemu.
Jakie są różnice między maszynami pneumatycznymi a hydraulicznymi
Maszyny pneumatyczne i hydrauliczne to dwa różne typy systemów napędowych, które mają swoje unikalne cechy i zastosowania. Główna różnica między nimi polega na medium roboczym – maszyny pneumatyczne wykorzystują sprężone powietrze, podczas gdy maszyny hydrauliczne operują cieczą, najczęściej olejem hydraulicznym. Ta różnica ma istotny wpływ na charakterystykę działania obu systemów. Maszyny pneumatyczne są zazwyczaj lżejsze i prostsze w budowie, co sprawia, że są łatwiejsze do transportu i instalacji. Dodatkowo ich działanie jest bardziej elastyczne i szybkie, co czyni je idealnymi do aplikacji wymagających dynamicznych ruchów. Z drugiej strony maszyny hydrauliczne charakteryzują się większą siłą i momentem obrotowym, co sprawia, że są bardziej odpowiednie do ciężkich prac przemysłowych oraz tam, gdzie wymagana jest duża moc. Kolejną różnicą jest koszt eksploatacji – sprężone powietrze jest często droższe w produkcji niż olej hydrauliczny, co może wpływać na decyzję o wyborze jednego z tych rozwiązań.
Jakie są kluczowe aspekty bezpieczeństwa w maszynach pneumatycznych
Bezpieczeństwo w kontekście maszyn pneumatycznych jest niezwykle istotnym zagadnieniem, które należy brać pod uwagę już na etapie projektowania oraz eksploatacji tych urządzeń. Przede wszystkim ważne jest zapewnienie odpowiednich norm ciśnienia roboczego oraz regularne kontrole stanu technicznego wszystkich komponentów systemu. Wszelkie uszkodzenia lub zużycie elementów mogą prowadzić do niebezpiecznych sytuacji, dlatego zaleca się stosowanie zaworów bezpieczeństwa oraz manometrów do monitorowania ciśnienia w czasie rzeczywistym. Kolejnym kluczowym aspektem jest szkolenie pracowników obsługujących maszyny pneumatyczne. Powinni oni znać zasady bezpiecznej pracy oraz umieć rozpoznać potencjalne zagrożenia związane z użytkowaniem sprzętu. Dobrą praktyką jest również stosowanie osłon ochronnych na ruchome części maszyn oraz wdrażanie procedur awaryjnych na wypadek nieprzewidzianych sytuacji. Niezwykle istotne jest także regularne serwisowanie urządzeń przez wykwalifikowany personel, co pozwala na szybką identyfikację ewentualnych usterek i ich natychmiastowe usunięcie.
Jakie są przyszłe kierunki rozwoju technologii maszyn pneumatycznych
Przyszłość technologii maszyn pneumatycznych zapowiada się obiecująco dzięki ciągłemu rozwojowi innowacyjnych rozwiązań inżynieryjnych oraz integracji z nowoczesnymi technologiami cyfrowymi. Jednym z głównych kierunków rozwoju jest automatyzacja procesów produkcyjnych poprzez zastosowanie sztucznej inteligencji oraz robotyzacji. Dzięki temu możliwe będzie zwiększenie precyzji oraz efektywności działania maszyn pneumatycznych w różnych aplikacjach przemysłowych. Ponadto rozwój materiałów kompozytowych i nanotechnologii przyczyni się do poprawy trwałości i wydajności komponentów pneumatycznych, co wpłynie na ich dłuższą żywotność oraz mniejsze koszty eksploatacji. Wprowadzenie inteligentnych systemów monitorowania pozwoli na bieżąco analizować dane dotyczące pracy maszyn, co umożliwi optymalizację procesów oraz przewidywanie awarii zanim one nastąpią. Również rozwój technologii 3D drukowania otworzy nowe możliwości w zakresie produkcji części zamiennych i prototypowania nowych rozwiązań konstrukcyjnych.
Jakie są koszty eksploatacji maszyn pneumatycznych
Koszty eksploatacji maszyn pneumatycznych mogą być znaczące i powinny być dokładnie analizowane przed podjęciem decyzji o ich wdrożeniu w danym zakładzie produkcyjnym. Główne składowe tych kosztów obejmują zużycie energii potrzebnej do sprężania powietrza, konserwację komponentów oraz ewentualne naprawy awaryjne. Koszt energii elektrycznej związany z działaniem sprężarek może stanowić dużą część budżetu operacyjnego firmy, zwłaszcza jeśli maszyny pracują przez długie godziny lub w trybie ciągłym. Dlatego warto inwestować w nowoczesne sprężarki o wysokiej efektywności energetycznej oraz systemy zarządzania energią, które mogą pomóc w redukcji tych kosztów. Koszty konserwacji również nie powinny być bagatelizowane; regularne przeglądy techniczne oraz wymiana zużytych części są niezbędne dla zapewnienia prawidłowego funkcjonowania maszyn. Dodatkowo warto uwzględnić koszty związane z ewentualnymi przestojami produkcyjnymi spowodowanymi awariami lub koniecznością przeprowadzania napraw.