Destylacja rozpuszczalników to proces, który polega na oddzieleniu składników mieszaniny na podstawie różnicy w ich temperaturach wrzenia. W praktyce oznacza to, że ciecz, która ma niższą temperaturę wrzenia, paruje jako pierwsza, a następnie para ta jest schładzana i skraplana z powrotem do postaci cieczy. Proces ten jest szeroko stosowany w chemii oraz przemyśle, gdzie oczyszczenie substancji chemicznych jest kluczowe. Destylacja może być przeprowadzana w różnych warunkach, w tym pod ciśnieniem atmosferycznym lub w warunkach próżniowych, co pozwala na obniżenie temperatury wrzenia niektórych substancji. W przypadku rozpuszczalników organicznych, takich jak etanol czy aceton, destylacja jest często wykorzystywana do ich oczyszczania lub odzyskiwania z odpadów przemysłowych. Kluczowym elementem tego procesu jest kolumna destylacyjna, która umożliwia wielokrotne skraplanie i parowanie substancji, co zwiększa efektywność separacji.
Jakie są rodzaje destylacji rozpuszczalników i ich zastosowania
W kontekście destylacji rozpuszczalników wyróżnia się kilka podstawowych metod, które są dostosowane do specyficznych potrzeb i właściwości substancji. Najpopularniejszą formą jest destylacja prosta, która znajduje zastosowanie przy separacji składników o znacznie różniących się temperaturach wrzenia. Jest to metoda stosunkowo łatwa do przeprowadzenia i często wykorzystywana w laboratoriach do oczyszczania jednoskładnikowych roztworów. Kolejnym rodzajem jest destylacja frakcyjna, która pozwala na oddzielenie kilku składników o zbliżonych temperaturach wrzenia. Proces ten wymaga użycia kolumny frakcyjnej, która zwiększa powierzchnię wymiany ciepła i umożliwia lepszą separację. Destylacja próżniowa to kolejna technika, która jest stosowana do destylacji substancji termolabilnych, które mogą ulegać degradacji w wysokich temperaturach. Dzięki obniżonemu ciśnieniu możliwe jest przeprowadzenie procesu w niższej temperaturze. Ostatnim rodzajem jest destylacja azeotropowa, która polega na dodaniu innego rozpuszczalnika w celu zmiany właściwości azeotropu i umożliwienia dalszej separacji składników.
Jakie są zalety i ograniczenia destylacji rozpuszczalników
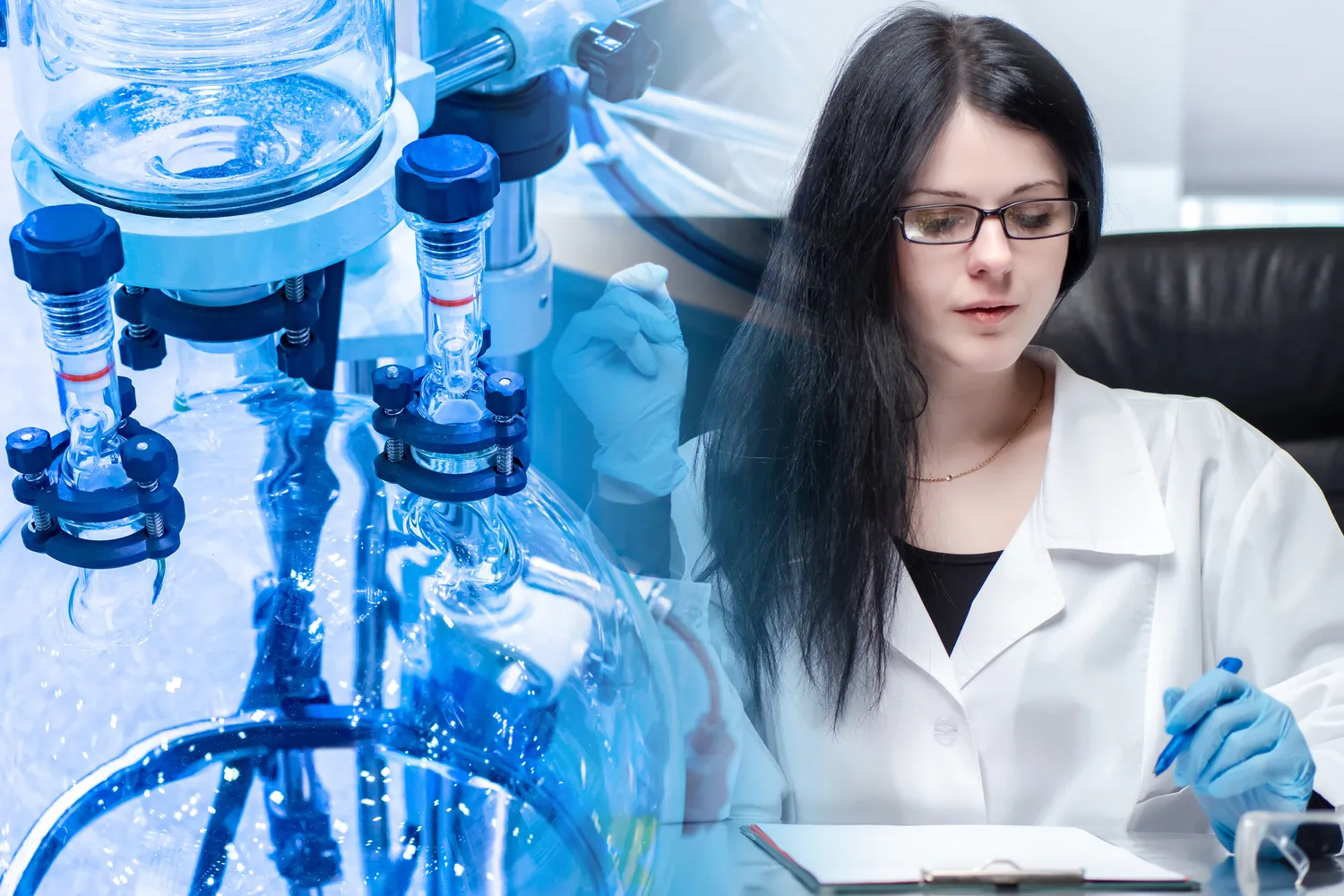
Destylacja rozpuszczalników ma wiele zalet, które sprawiają, że jest popularną metodą oczyszczania i separacji substancji chemicznych. Jedną z głównych korzyści jest jej efektywność – proces ten pozwala na uzyskanie wysokiej czystości produktów końcowych poprzez oddzielenie niepożądanych składników. Dodatkowo destylacja jest metodą stosunkowo prostą do wdrożenia zarówno w laboratoriach badawczych, jak i w przemyśle. Możliwość skalowania procesu sprawia, że można go dostosować do różnych potrzeb produkcyjnych. Jednakże istnieją również pewne ograniczenia związane z tą metodą. Przede wszystkim nie wszystkie substancje można skutecznie oddzielić za pomocą destylacji – szczególnie te o bardzo zbliżonych temperaturach wrzenia mogą stanowić wyzwanie dla tej techniki. Ponadto proces ten może być czasochłonny i wymaga odpowiedniego wyposażenia oraz doświadczenia operatora. Koszty związane z budową instalacji destylacyjnej oraz zużyciem energii również mogą być znaczące.
Jakie są najczęstsze błędy podczas destylacji rozpuszczalników
Podczas przeprowadzania procesu destylacji rozpuszczalników istnieje wiele pułapek i błędów, które mogą prowadzić do nieefektywności lub nawet uszkodzeń sprzętu. Jednym z najczęstszych błędów jest niewłaściwe ustawienie temperatury grzania. Zbyt wysoka temperatura może prowadzić do przegrzewania się cieczy oraz powstawania niepożądanych produktów ubocznych, co negatywnie wpływa na jakość końcowego produktu. Kolejnym istotnym aspektem jest niewłaściwe użycie kolumny frakcyjnej – jeśli nie zostanie ona odpowiednio dobrana do rodzaju mieszaniny, efektywność separacji może być znacznie obniżona. Należy także pamiętać o odpowiedniej kontroli ciśnienia podczas destylacji próżniowej; jego niewłaściwe ustawienie może prowadzić do nieefektywnego procesu lub uszkodzenia sprzętu. Często spotykanym problemem jest również brak odpowiedniej kalibracji sprzętu pomiarowego, co może skutkować błędnymi wynikami pomiarów temperatury czy ciśnienia. Warto również zwrócić uwagę na czystość używanych materiałów – zanieczyszczenia mogą wpłynąć na wyniki procesu oraz jakość końcowego produktu.
Jakie są zastosowania destylacji rozpuszczalników w przemyśle
Destylacja rozpuszczalników odgrywa kluczową rolę w wielu gałęziach przemysłu, gdzie czystość substancji chemicznych jest niezbędna do zapewnienia wysokiej jakości produktów. W przemyśle chemicznym destylacja jest wykorzystywana do oczyszczania surowców oraz produktów pośrednich, co pozwala na uzyskanie substancji o odpowiednich właściwościach fizykochemicznych. Przykładem może być produkcja alkoholi, gdzie destylacja etanolu z fermentowanych surowców roślinnych jest podstawowym procesem technologicznym. W przemyśle farmaceutycznym destylacja jest stosowana do oczyszczania substancji czynnych oraz rozpuszczalników, co ma kluczowe znaczenie dla bezpieczeństwa i skuteczności leków. Również w przemyśle petrochemicznym destylacja frakcyjna jest niezbędna do separacji różnych frakcji ropy naftowej, co umożliwia produkcję paliw oraz innych produktów chemicznych. W laboratoriach badawczych destylacja jest często wykorzystywana do przygotowywania czystych rozpuszczalników oraz do analizy składników mieszanin, co pozwala na prowadzenie różnorodnych badań naukowych.
Jakie są nowoczesne technologie w destylacji rozpuszczalników
W ostatnich latach rozwój technologii przyczynił się do znacznego usprawnienia procesów destylacji rozpuszczalników. Jednym z najważniejszych osiągnięć jest wprowadzenie systemów automatyzacji, które pozwalają na precyzyjne kontrolowanie parametrów procesu, takich jak temperatura czy ciśnienie. Dzięki temu możliwe jest zwiększenie efektywności separacji oraz poprawa jakości końcowego produktu. Nowoczesne kolumny destylacyjne wyposażone są w zaawansowane systemy monitorowania, które umożliwiają bieżącą analizę składu mieszaniny i dostosowywanie warunków pracy w czasie rzeczywistym. Kolejnym innowacyjnym rozwiązaniem są technologie membranowe, które mogą być stosowane jako alternatywa dla tradycyjnej destylacji. Membrany pozwalają na selektywne oddzielanie składników na podstawie ich wielkości lub właściwości chemicznych, co może prowadzić do oszczędności energii i zmniejszenia kosztów operacyjnych. Warto również wspomnieć o zastosowaniu technologii mikrofalowej w procesach destylacyjnych, która umożliwia szybsze podgrzewanie cieczy i efektywniejsze przeprowadzanie procesu.
Jakie są różnice między destylacją a innymi metodami separacji
Destylacja rozpuszczalników to jedna z wielu metod separacji składników mieszanin, jednak różni się ona od innych technik zarówno pod względem zasad działania, jak i zastosowań. Na przykład ekstrakcja to metoda polegająca na przenoszeniu składnika z jednej fazy do drugiej, często wykorzystująca różnice w rozpuszczalności substancji w różnych rozpuszczalnikach. Ekstrakcja może być bardziej efektywna w przypadku substancji o podobnych temperaturach wrzenia, gdzie destylacja mogłaby być mniej skuteczna. Z kolei chromatografia to technika separacji oparta na różnicach w adsorpcji składników na stałym nośniku; jest szczególnie przydatna w analizie chemicznej i może prowadzić do uzyskania bardzo czystych frakcji. Filtracja to inna metoda separacji, która polega na oddzieleniu ciał stałych od cieczy lub gazów za pomocą porowatego materiału; jest to technika stosunkowo prosta, ale nie zawsze wystarczająco dokładna dla substancji chemicznych wymagających wysokiej czystości. Każda z tych metod ma swoje unikalne zalety i ograniczenia, a wybór odpowiedniej techniki zależy od specyfiki procesu oraz właściwości separowanych składników.
Jakie są przyszłe kierunki rozwoju technologii destylacji
Przyszłość technologii destylacji rozpuszczalników zapowiada się obiecująco dzięki ciągłemu postępowi naukowemu oraz innowacjom technologicznym. Jednym z kluczowych kierunków rozwoju jest dążenie do zwiększenia efektywności energetycznej procesów destylacyjnych poprzez zastosowanie nowych materiałów oraz konstrukcji kolumn destylacyjnych. Badania nad nanomateriałami oraz ich zastosowaniem w procesach separacyjnych mogą prowadzić do znacznego zwiększenia wydajności procesów oraz obniżenia kosztów operacyjnych. Również rozwój technologii symulacyjnych i modelowania komputerowego otwiera nowe możliwości optymalizacji procesów destylacyjnych jeszcze przed ich wdrożeniem w praktyce. Innowacyjne podejścia do zarządzania odpadami powstałymi podczas procesu destylacji mogą również przyczynić się do zmniejszenia wpływu na środowisko naturalne. Warto również zauważyć rosnące zainteresowanie zrównoważonym rozwojem i ekologicznymi metodami produkcji, co skłania przemysł do poszukiwania bardziej przyjaznych dla środowiska alternatyw dla tradycyjnej destylacji.
Jakie są najważniejsze aspekty bezpieczeństwa podczas destylacji
Bezpieczeństwo podczas przeprowadzania procesów destylacji rozpuszczalników jest niezwykle istotne ze względu na potencjalne zagrożenia związane z używanymi substancjami chemicznymi oraz wysokimi temperaturami. Przede wszystkim kluczowe jest przestrzeganie zasad BHP oraz korzystanie z odpowiedniego wyposażenia ochronnego, takiego jak rękawice czy gogle ochronne. Ważne jest również zapewnienie odpowiedniej wentylacji w pomieszczeniu, gdzie odbywa się proces destylacji, aby uniknąć gromadzenia się oparów szkodliwych substancji chemicznych. Należy również zwrócić uwagę na właściwe oznakowanie wszystkich używanych substancji oraz ich przechowywanie zgodnie z obowiązującymi normami bezpieczeństwa. Regularne przeglądy sprzętu oraz konserwacja instalacji są niezbędne dla zapewnienia ich prawidłowego funkcjonowania i minimalizacji ryzyka awarii. W przypadku pracy z substancjami łatwopalnymi konieczne jest stosowanie odpowiednich środków ostrożności, takich jak unikanie źródeł zapłonu czy stosowanie sprzętu odpornych na działanie wysokich temperatur.